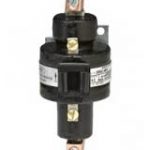
SINGLE POLE
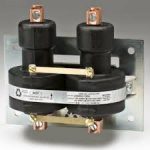
DOUBLE POLE
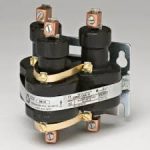
TRIPLE POLE
WHAT IS A MERCURY CONTACTOR:
Mercury Relays (Mercury Contactors) are all designed and built to meet the most exacting demands of industry. They have won their high place in the electrical field by doing the tough and tricky jobs that ordinary equipment could at best do in an uncertain manner (especially resistive heating). They have proved their ability to stand up under the most adverse conditions of temperature, dust and moisture, in all types of applications. All the care required for the manufacture of high-grade instruments is used in the manufacture of the switches. All switch parts are specially cleaned, and contamination is avoided by use of tweezers, gloves, etc., when making assemblies.
Mercury Relays (Mercury Contactors) are hermetically sealed with high quality glass to metal seals.
The stainless steel tube is totally encapsulated in high grade UL approved epoxy to prevent moisture damage and voltage breakdown through the protective coating.
The coils are wound on compact nylon bobbins and molded onto the metal tube to provide minimum power loss. This allows for low coil power required to actuate the contactor. This also enables the units to handle high loads with minimum de-rating due to higher ambient temperatures.
Inert gases internally prevent excessive arcing between the mercury and the electrodes which enables the unit to function for millions of cycles with very low contact resistance, and minimum deterioration of the internal parts.
Available in all standard coil voltages, in single pole, two pole and three pole arrangements. Other coil voltages available upon request.
In multiple pole units each tube is actuated by its own coil. This eliminates pull-in variation between contact tubes, assuring consistent switching.
HOW IS A MERCURY TO METAL CONTACTOR DESIGNED:
The mercury relays (mercury contactors) load terminals are isolated from each other by the glass in the hermetic seal. “The plunger assembly”, which includes the ceramic insulator, the magnetic sleeve and related parts, floats on the mercury pool. When the coil is powered causing a magnetic field, the plunger assembly is pulled down into the mercury pool which is in turn displaced and moved up to make contact with the electrode, closing the circuit between the top and bottom load terminal, which is connected to the stainless steel can.
To make the unit function as a “Hybrid” time delay, we add a solid state circuit to the coil to delay the power to the coil.
For constant duty applications, a return spring is used in place of the buffer spring. Contact the factory.
ADVANTAGES OVER ELECTROMECHANICAL AND SOLID STATE RELAYS:
-
- Superior Performance and Reliability
-
- Long life
- Durable
- Compact Size
- Low, Predictable Contact Resistance
- Reduced RFI for Improved Interface Capability
- Handles a Variety of Loads
-
- Increases design flexibility
- Rapid On-Off Cycling Capability
-
- Mercury quickly dissipates contact heat
- Low Coil Power Requirements
- Minimal Derating Due to Higher Ambient Temperatures
- Quiet Action
- DESIGN and CONSTRUCTIONContacts are within a hermetically sealed steel body
-
-
- Impervious to adverse conditions
- No external arcing
- Arcing is in a gaseous atmosphere
-
- Quenches the arc
- Extends relay life
- Only one moving part (the plunger)
-
- No buttons to pit, weld or burn out
- One coil for each set of contacts
-
- Assures consistent switching
- Minimizes pull-in variation between contacts
- Epoxy encapsulated
-
- Moisture resistant
- High dielectric strength
- Permanently fixes contacts to coil; eliminating possible misalignment
- Helps dissipate heat and noise
- Rugged (impact resistant)
-
- BENEFITS
-
- Reduction of Operational and Maintenance costs
- Increases Utilization and Productivity of Equipment
-
- By reducing down-time
- Installation and service is a routine operation
-
- Simple to install
- No sophisticated equipment is required
- Easy to trouble-shoot
Applications:
Auditorium Lighting
Copy Equipment
Dimmer Controls
Display Signs
Emergency Lighting
Flood Lights
High Intensity Lamps
Hospital Lighting
Lighting Test Panels
Mercury Vapor Lamps
Parking Lots
Photography Lighting
Scoreboards
Sodium Vapor Lamps
Stage Lighting
Street Lighting
Tower Control
Traffic Signal
Tungsten Lamps
Air Conditioning
Alarm Systems
Automatic Door Closers
Battery Chargers
Blue Print Machines
Copiers
Computer Power Supplies
Corrosive Locations
Dusty, Oily Locations
Dry Cleaning Equipment
Energy Management Systems
Farm Incubators and Brooders
High Cycle Rate Applications
Low Voltage Switching
Marking Equipment
Engraving Equipment
Motor Starting
Soldering Systems
Telephone Switching
Test Panels
Vapor De-greasers
X-Ray Machine Controls
Baseboard Heaters
Blow Molding
Cabinet Heaters
Chemical Tank Heaters
Curing Furnaces
Drying Ovens
Duct Heaters
Film Packaging
Glass Furnaces
Heat Lamps
Heat Sealing Machines
Induction Heater
Industrial Ovens
Infrared Heaters
Ink Drying
Ink Heating
Injection Molding Machines
Kilns
Lab Ovens
Packaging Equipment
Plastic Extruder
Quartz Heaters
Radiant Heaters
Roof Top Heating
Shrink Tunnels
Unit Heaters
Vacuum Forming
FOOD INDUSTRY EQUIPMENT (HEATERS)
Baking Ovens
Coffee Urns
Deep Fryers
Dishwashers
Electric Grills
Electric Ranges
Pizza Ovens
Steam Generators
SPECIALTY APPLICATIONS
Capacitor Discharge Systems
Hazardous Locations
Phase Converters
Tower Control